Table of Contents
Would you like to improve your working conditions in your workplace? Are you looking for the best solution to not waste any time on nonsensical things and focus on what’s important? You should know about the 5S Methodology!
5S Methodology, also called 5S Implementation, is one of the easiest ways to kickstart lean in your company. You can apply it to both physical and digital spaces.
It requires total employee participation and gives a lot of benefits. A 5S implementation helps to define the first rules to eliminate waste and maintain an efficient, safe, and clean work environment.
This technique was originally created by Taiichi Ohno as a concept of workplace organization in a Toyota factory in the 1950s. Later, the concept evolved to the 5S.
5S is tightly connected to Kaizen, which we discussed as a management philosophy before.
5S – 5 Work Environment Goals
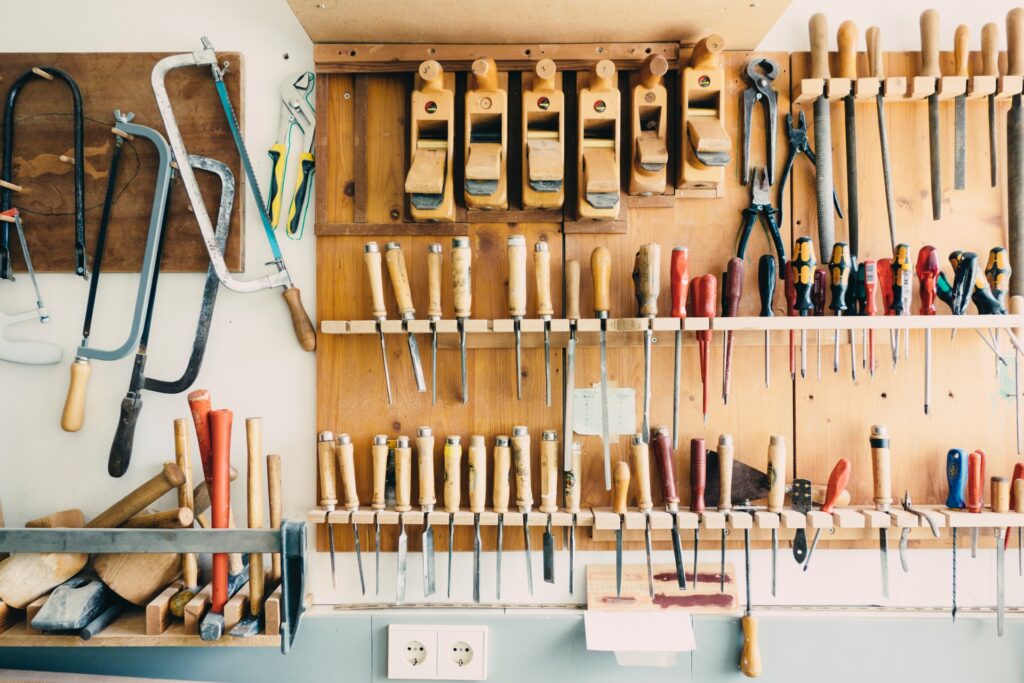
The name 5S comes from five Japanese words and every “S” is a goal unto itself.
Seiri: Sort
Separate required tools, materials, and instructions from those that are not needed. Clean a workplace of what is unnecessary.
Seiton: Store
Furnish the workplace in an efficient way. Sort and organize all tools, equipment, files, data, and resources for quick and easy location. Label all storage locations, tools, and equipment.
Seiso: Shine
Keep a workplace very clean, remove all trash and dirt.
Seiketsu: Standardize
Engage employees to systematically perform steps 1, 2, and 3 and to maintain the workplace in perfect condition as a standard process.
Shitsuke: Sustain
Make 5S part of your culture, and incorporate it into the corporate philosophy. Make 5S one of your organizational values so that everyone develops 5S as a habit.
Advantages of Adopting 5S
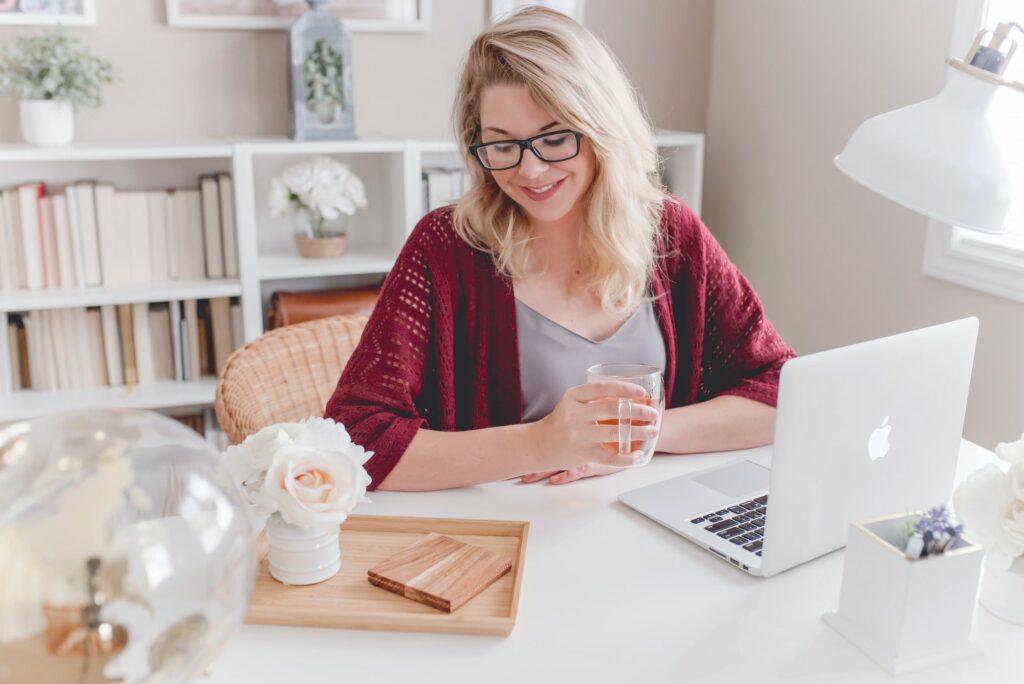
By implementing the 5S method you will find many improvements in different areas.
First, the working condition and the motivation of the employees will increase because it is so much more enjoyable to work in a clean workplace.
The methodology encourages self-discipline. Employees acquire self-discipline as they need to maintain the standards (put the tools pack in their positions, do daily cleaning, etc).
All personnel will save a lot of energy. . Everybody will be able to focus on important things and will not waste time.
And a lot of space will be saved because the removal of unwanted items and organizing the necessary materials release space.
The risk of accidents will be smaller. 5S helps to create a safe workplace by preventing accidents caused by mess and negligence.
5S and Remote Work
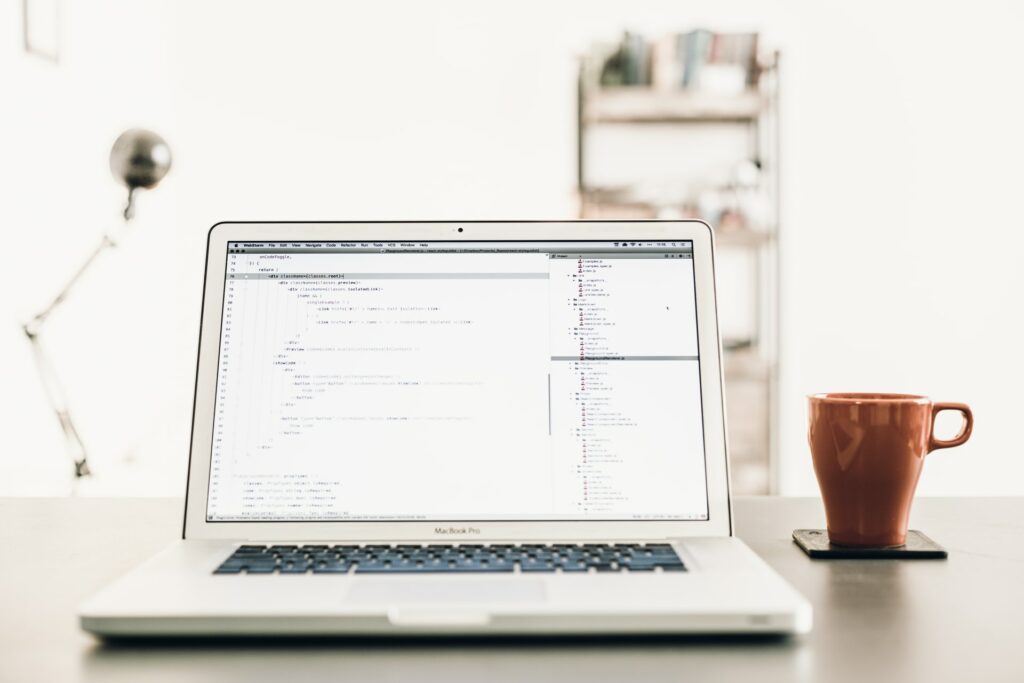
The 5S methodology was designed for factories, but it’s still very much relevant for office work. Even when we are doing or jobs remotely.
Workplace organization is important whatever the workplace. Keeping the home office/desk cleaner helps focus on work, and thus improves work/life balance. If you work at home, maintaining a designated workspace can help create a boundary between work items and home items.
Further, the condition of the workplace has a really significant impact on the way we work. When our space is in a mess, so do we.
But that’s not all. In today’s work environment almost everything is digital. Our computer is like an extension of our work desk. As such, the 5S approach can be applied to your electronic files using the same steps:
- Delete files you don’t really need. For example, remove old downloads and clean the desktop
- Order software, notes, and bookmarks in a logical manner that is easy to access and modify
- Properly maintain your disk drives and network, thus avoiding interruptions while you work
- Standardize the folder and filenames to make it easy for others to find them. Instead of “1 – copy.pdf”, prefer “main_project_asset.pdf”, for example
Managers should advocate 5S to their remote teams. They should initiate and participate in all implementation processes and, after all, give a good example. For example, they can show a picture of their workplace or introduce how to store data so it can be found quickly.
Employees should make it a part of their daily work and not an action forced upon them.
This is something we practice daily at Kambu. Learn more about us at Kambu!
Conclusion
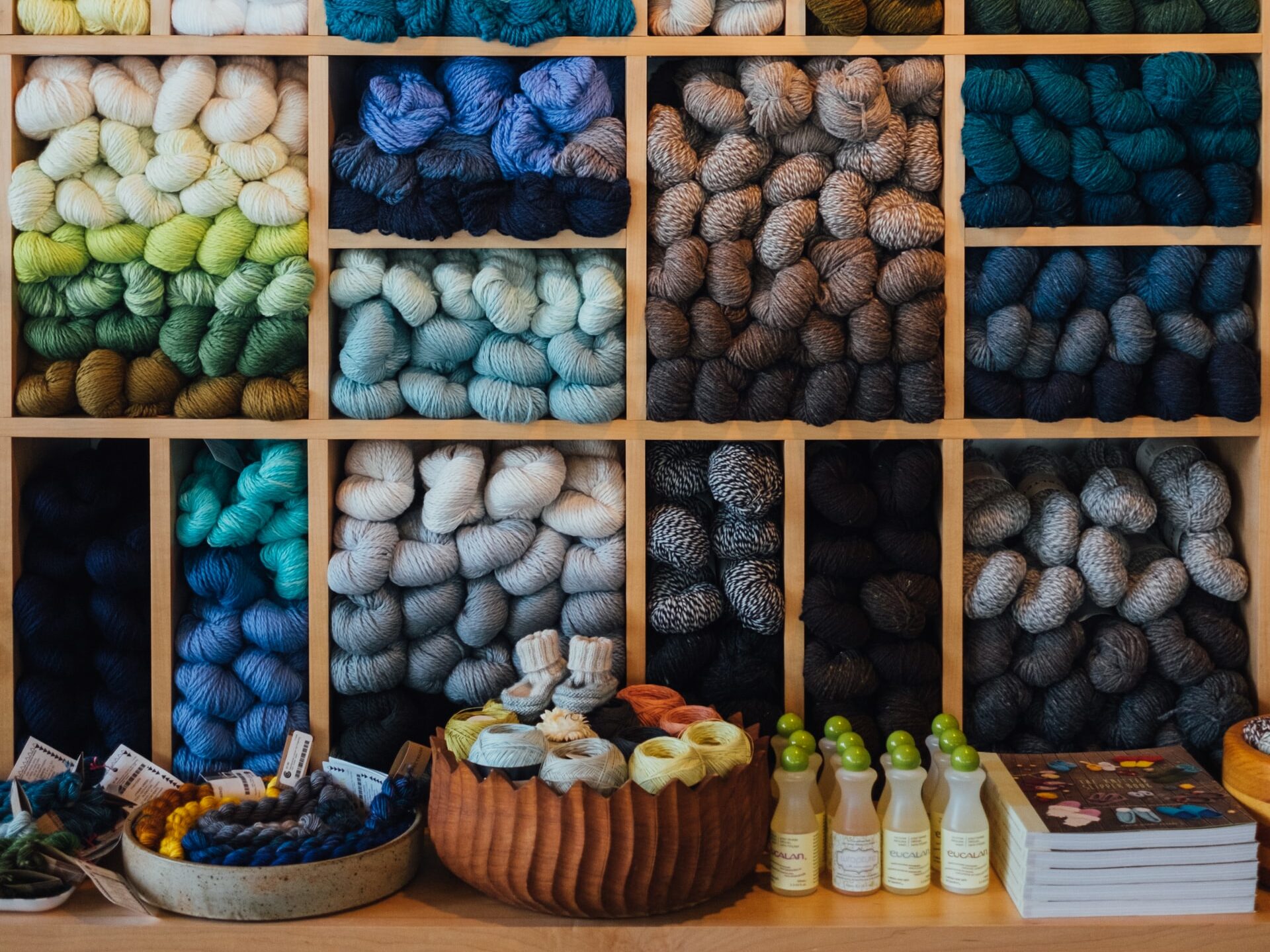
The 5S methodology seems to be a trivial practice but you have to answer the question: do you really have order and standards in your workplace?
We often don’t realize how much time we spend looking for things we need for work in a maze of others we don’t longer need for months. Saving time is the most important aspect!